The Southern Standard had a chance to ask Newell Brands senior manager of corporate communications Danielle Clark some questions about the company and its facility on Cadillac Lane in McMinnville.
Learning more about Newell Brands
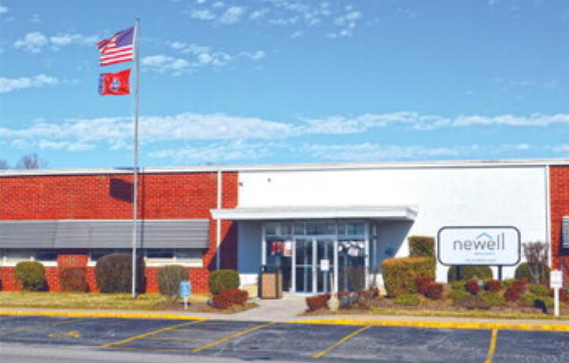
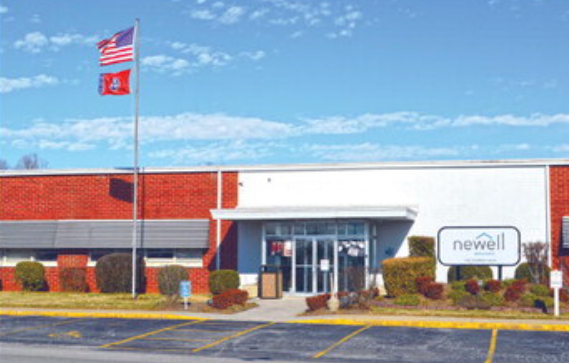